Continuous blending processes for the production of lube oils – a dream for increasing efficiency or just an empty promise.
The appropriate process for manufacturing lube oils
Continuous manufacturing processes have gained considerable importance in various industries, including the production of lube oils. This report examines the advantages and use of continuous manufacturing processes in the design of Lube Oil Blending Plants (LOBP).
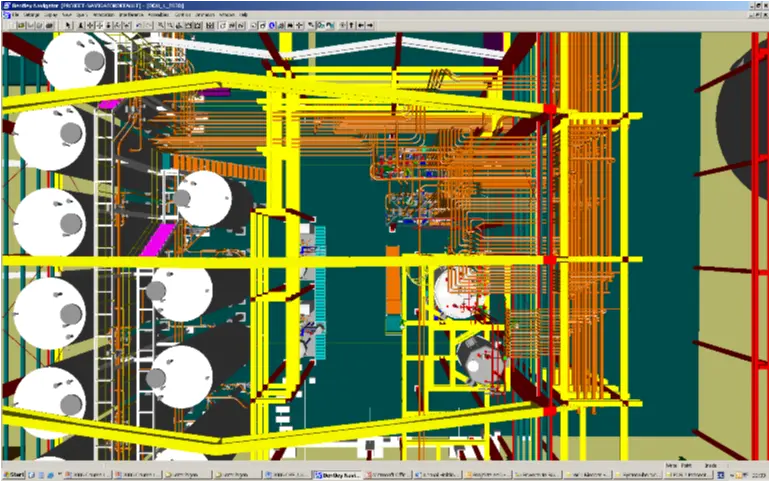
Fig. 1: Planning a LOBP with SMB and ABB applications
Choosing the right production process – continuous or batch blender?
Let’s get straight to the point. The continuous processes to produce lube oils make an important contribution to the efficient production of lubricants in LOBPs.
The portfolio of a typical lubricant producer usually comprises hundreds of individual formulations, which must be incorporated into the manufacturing processes in an economically and technically optimal way. Despite the large number of formulations, in practice it turns out that only a few formulations make up a large part of the production volume. For this limited number of formulations with large production volumes per batch, a continuous process makes sense.
Basically, the rule is:
- For large batch volumes (appr. > 50 tons per batch), the use of a continuous process makes sense.
- Smaller batch sizes are usually produced in discontinuous batch blenders.
The selection of the right production system is carried out with the help of a business analysis of the overall production, the so-called ‘plant improvement analysis’, which is described elsewhere in this blog.
This analysis calculates the required numbers and sizes of discontinuous batch blenders, the so called Automatic Batch Blender (ABB) and continuous production systems, the Simultaneous Metering Blender (SMB) or the In-Line Blender (ILB).
With the continuous systems of SMB and ILB, it is very easy to continuously produce product sizes from 100 to 200 tons or even more.
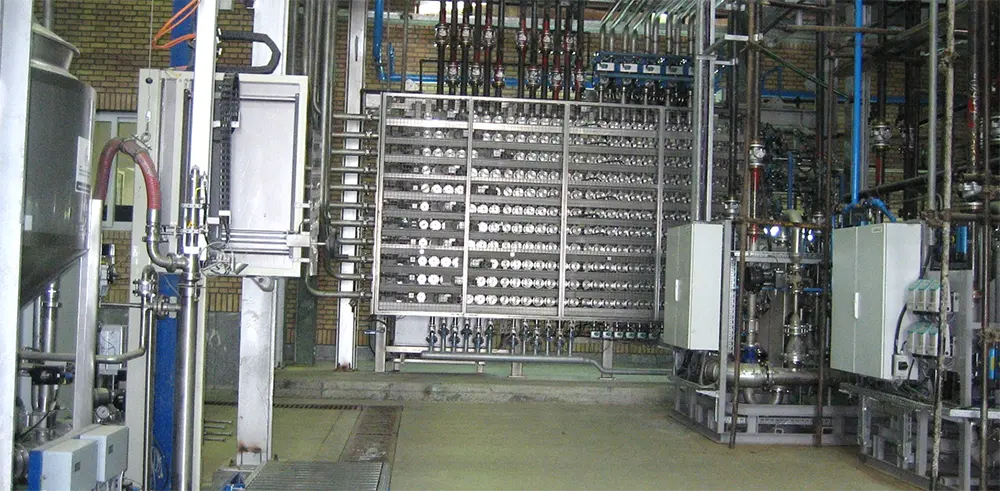
Fig. 2: Lube Oil Blending Plant (LOBP) with DDU, matrix manifold and 2 simultaneous metering blenders (SMB)
SMB und ILB explained
The Simultaneous-Metering-Blender (SMB)
For the production of lubricants, a distinction is usually made between the simultaneous metering blender (SMB) and the in-line blender (ILB), although the two names are often misleading and invite confusion.
During production with the SMB, the liquid raw materials (base oils, additives and small quantities) are delivered one after the other via a transfer pipe into a finished product tank. The raw materials are fed into the transfer pipe either directly from storage tanks or alternatively from smaller cocktail mixers or drums/IBCs. They can also be pumped into the SMB from drum decanting units (DDU). The quantity of each individual component is measured using massflow meters, which can detect the end point of the addition of each individual raw material very precisely.
Depending on the flow speed and viscosity, the different raw materials in the SMB are distributed via collectors and a few feed lines to the transfer line. The feed lines differ in diameter and each contains a mass flow meter to detect the end point of the dosing of each individual formulation component.
If the base oils still need to be heated, this process step is also carried out continuously in the SMB by switching on a heat exchanger while the base oils are being dosed into the finished product tanks.
The formulation components are thus transferred sequentially one after the other into a finished product tank. In this tank, all formulation components are mixed to form the finished lube oil. Blending is a simple process engineering task and can also be carried out in large tanks using side-mounted agitators.
The advantage of this production method is the very fast and very precise dosing of large quantities of raw materials with simultaneous heating of the base oils in a finished product tank, in which the blending can take place separately. Once dosing is complete, the SMB is immediately available for further formulations. The SMB is therefore much faster than a discontinuous batch blender. The batch times are much shorter.
In discontinuous batch processes, the formulation must first be completed after dosing before dosing can start again. In addition, heating in blending vessels via external half pipe coils take considerably longer than in efficient plate heat exchangers in the SMB.
The disadvantage of the SMB is its limited flexibility. In principle, of course, only those components can be dosed that are also connected to the SMB. A ‘cocktail mixer’ on the SMB can serve as a workaround, which can flexibly receive all types of drum goods or small quantities and dose them onto the SMB.
The SMB is cleaned using a pigging system, which cleans the transfer line from the SMB to the finished product tanks with minimal residue. Only residual quantities between the raw material collector, the mass flow meter and the connection to the feed line cannot be 100% avoided, even after compressed air treatment.
The SMB is built as a space-saving, stand-alone platform on which all the necessary units for dosing and heating the raw materials are housed. As a plug’n play unit, the installation of such a skid unit is quick and easy.
The In-Line-Blender (ILB)
When producing lube oils with the ILB, all formulation components are simultaneously dosed into a transfer line in the correct mixing ratio. Here too, the raw materials can be transferred directly from storage vessels or from cocktail mixers. A transfer of additives from a drum decanting unit (DDU) is not suitable for the ILB, as the additive from the DDU is only available discontinuously.
A separate feed line and a separate mass flow meter are required for each of the raw materials dosed in parallel. This can easily mean that three to four times as many feed lines are required compared to the SMB. The costs for an ILB are therefore generally higher than for an SMB skid. The base oils can also be heated in an ILB before the additive components are added. In addition, a static or dynamic in-line mixing device is installed in the ILB so that all components are completely mixed at the end of the unit.
Like the SMB, the ILB is built and supplied as an independent platform so that it can also be easily installed in existing production systems.
The clear advantage of the ILB is that the lube oil is ready to use as soon as it leaves the ILB unit. All raw material components are added in parallel in the correct ratio and mixed immediately. A finished product tank is theoretically no longer required for mixing the raw material components.
However, the reality is that, for logistical reasons, the finished lubricant is pumped from the ILB skid into a finished product tank in which the finished product is waiting to be filled. It should also be noted that the ILB has a certain run-in phase lasting several minutes, during which all components have to start up and the correct quantity ratio has to be found. The correct ratio of the raw materials to each other cannot be guaranteed during this running-in phase. Either the lubricant from this run-in phase is discharged separately as a loss or the material from the run-in phase is mixed with the rest of the batch in the finished product. This in turn requires a finished product tank. At the end of continuous production in the ILB, there may also be shifts in the ratio of raw materials, resulting in off-spec finished products.
The quality assurance of the finished product in the ILB must also be considered. Continuous sampling is required and what happens with off-spec material? If the finished product tank is not available, remixing is no longer possible.
If it were possible to guarantee stable production in the ILB and avoid the finished product tank by filling directly into containers/trucks, then the ILB would be an unbeatable alternative as a continuous production unit. By eliminating the finished product tanks, the slightly higher investment compared to the SMB always pays off. However, if mixing has to take place due to the run-in and run-out quantities and a finished product tank is therefore necessary, then an investment in the ILB is always less profitable than in the SMB from a purely economic point of view.
Possible residual quantities in the ILB are minimized here through the use of pigging technology, but not completely avoided in the area of the feed lines. It is necessary to consider the residual quantities for each application.
The control system of the ILB must be evaluated separately. Due to the necessary, continuous dosing of the raw materials in the correct ratio, all mass flow meters must be continuously monitored by the control system and the other components must be adjusted and shut down accordingly if a delivery rate drops. If one component fails, the ILB operation is knocked out.
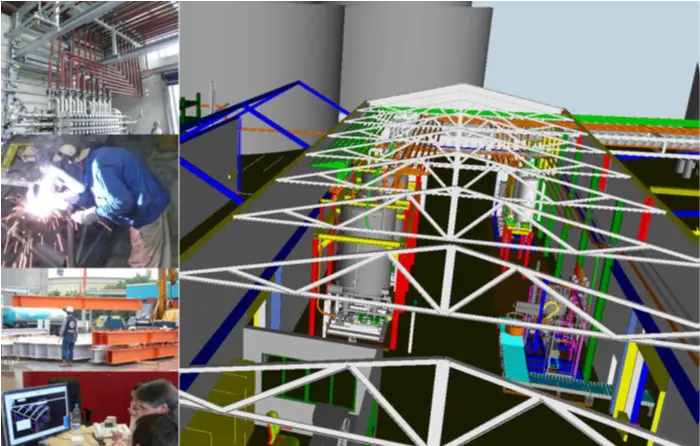
Fig. 5: Engineering of a complete Lube Oil Blending Plant (LOBP)
Conclusion
The philosophy of the In-Line Blender (ILB) with the immediate completion of the lube oil downstream of the blender in continuous operation sounds tempting. If the lube oil could be filled directly downstream of the ILB and finished product tanks could be dispensed with, then this production method would be the method of choice for large batch volumes. Compared to the SMB and especially the blending vessel, production times are considerably shorter.
In reality, however, it is not possible to dispense with finished product tanks. The run-in and run-out volumes as well as quality assurance of the finished products also currently still requires intermediate storage in order to have a buffer until quality release after the laboratory test or the possibility of readjusting the finished product.
The SMB is also able to produce large quantities of finished product continuously. However, this requires a finished product tank for mixing the sequentially added raw materials. This means that quality assurance and remixing in the finished product tank is possible at any time.
As the batch times in the SMB are considerably shorter than for comparable quantities from blending vessels, the SMB is the best choice for continuous production processes in lube oil production.
If it were possible to carry out quality management during production by the ILB in a secure manner and to ensure direct filling from the ILB, then the ILB process could play out its advantages and replace the SMB technology if the finished product tank is eliminated.