The perfect size of a production line – a business decision or a good gut feeling?
The way to the ‘Plant-Improvement-Analysis (PIA)’.
Not the gut feeling defines the batch size
What is the optimum batch size?
When expanding production facilities, the central question is often how large the new production unit should be designed. This usually involves batch reactors or continuous production units. The size of the production units determines all further design data of the production plant.
It is worth taking a look at the determination of the plant size in order to design according to the requirements, but not oversized.
If it would be possible to consider every single recipe of a production unit and to determine an optimal batch size for every single recipe, then a definition of the optimal reactor size for the complete set of recipes is possible.
This is exactly the approach taken by our ‘Plant Improvement Analysis (PIA)’. In PIA, a comprehensive, economic view of the production environment is developed for each recipe and the optimized batch size is defined according to economic considerations.
The optimal batch size describes the point at which the sum of storage and production costs (total costs) are minimal (see Fig. 1).
What factors influence the optimal batch size?
The amount of production costs when producing goods depends on the respective energy consumption (operating resources such as electricity or gas), possible setup costs for machines, the working time of operators or costs for laboratory analyses. These production costs must always be considered individually for each recipe.
In addition to production costs, storage costs are also incurred. Raw materials and finished products have to be stored, which results in physical storage costs as well as expenses for capital commitment.
Production and storage costs are two opposing cost blocks depending on the production volume (see Fig. 1).
The larger the production quantity, the lower the relative production costs. Reasons for this can be the same production time with a larger volume or lower laboratory costs per volume. At the same time, storage costs increase with larger production volumes due to increasing demand for storage facilities and higher expenses for capital commitment.
With PIA, the optimal production quantity of a batch (optimal batch size) is determined for each individual recipe of a production line as a function of the storage and production costs.
The result is a static simulation in which the economically optimal batch size for all recipes over a defined period of time will be calculated (e.g. annual demand) (see Fig. 2).
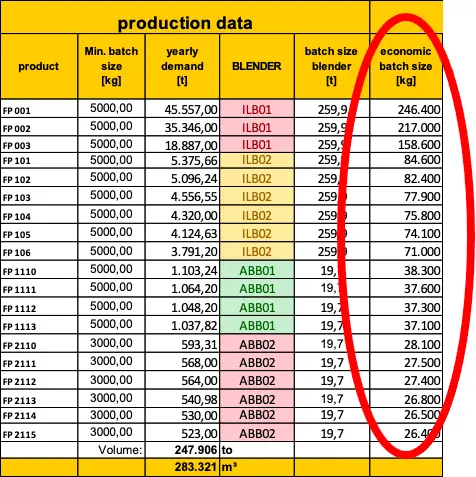
Fig. 2: Determination of the economic batch size according to PIA using the example of a Lube Oil Blending Plant (LOBP)
Mathematically, the optimal production quantity is determined according to the modified Andler formula (EOQ formula).
(Kurt Andler: Rationalisierung der Fabrikation und optimale Losgröße. Oldenbourg, München. 1929.)
In business management theory for determining optimal inventory levels, Andler’s formula is a well-known and applied model.
Adaptation of the PIA to side conditions
Side conditions from reality can influence the results coming from the mathematical simulation of the economically optimal production size.
For example, when defining the batch sizes, transport sizes, packaging sizes or also delivery bottlenecks of raw materials can play a role and influence the storage capacities or the batch sizes.
Therefore, an examination of the PIA results must be carried out for each recipe, considering the side conditions. Only after examination, the actual storage sizes for raw materials and finished products as well as the optimum batch sizes are finally determined.
Applications
Originally, the calculation method was developed for sizing in the production of article lots. The storage costs are compared to the setup costs and the economic batch size is determined.
We use the Plant Improvement Analysis (PIA) for economic batch sizing in the production of chemical and petrochemical products. In practice, we have used PIA for the design of optimal production facilities to produce lubricants (LOBP) and the assessment of synthetic resin plants (SRP).
For both applications, empirical values are available. Both, continuous production lines and discontinuous (batch) reaction and mixing processes can be considered.
In the application of PIA, the number and sizes of storage tanks and packaging units for raw materials and finished products are determined as well as the size and quantity of continuous or discontinuous production units.
From the PIA simulation, the material flow diagram and the process flow diagram are developed, in which the quantities and sizes of the storage and production tanks are represented, and also, the delivery of the raw materials and the filling of the finished products are defined (see Figs. 4 and 5).
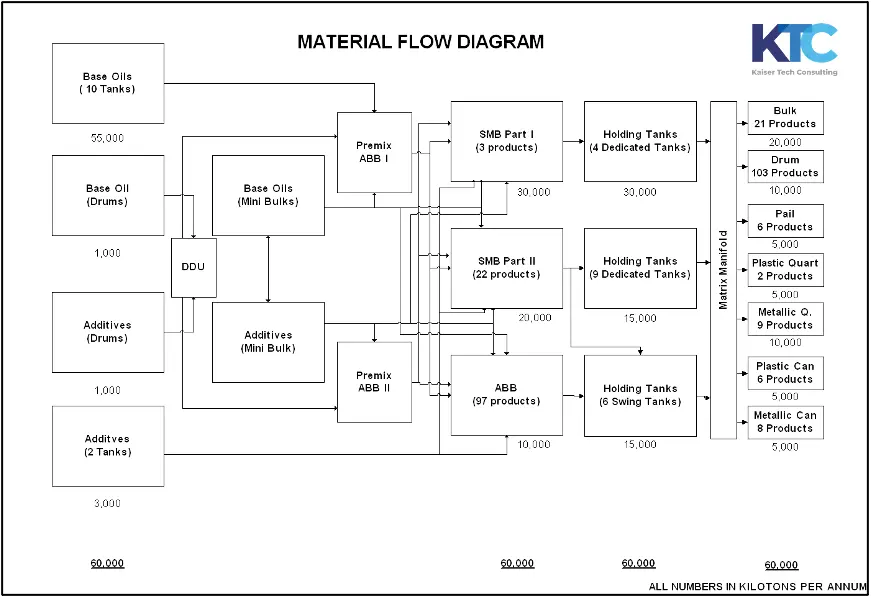
Fig. 4: Mass balance from PIA simulation for a Lube Oil Blending Plant (LOBP)
Management Summary
The determination of the optimal size for production units is the basis for the planning of new production facitlities (greenfield) or production expansions (greyfield).
The Plant Improvement Analysis (PIA) presented here provides a calculation of the optimum batch size based on economic data. The results of the PIA are upgraded with real side conditions.
Especially in the field of Synthetic Resin Plants (SRP) and Lube Oil Blending Plants (LOBP) the PIA has already been approved and successfully applied.
The analysis provides the size and number of necessary production units as well as the associated storage capacities for raw materials and finished products based on real data of each individual product of a production unit.
The PIA simulation is the basis for any process-engineering consideration and planning of a production plant on a economic basis, considering real data and interference factors. A cost-effective, fast and integral design of production plants.
For more information, please contact me at any time!