Die perfekte Größe eines Produktionsansatzes – Eine betriebswirtschaftliche Entscheidung oder doch ein gutes Bauchgefühl?
Der Weg zur ‘Plant-Improvement-Analyse (PIA)’
Nicht der Bauch definiert die Batchgröße
Was ist die optimale Batchgröße?
Bei der Erweiterung von Produktionsanlagen ist oftmals die zentrale Frage, wie groß die neue Produktionseinheit gewählt werden muss. Hier geht es in der Regel um Chargenreaktoren oder kontinuierliche Produktionseinheiten, deren Größe alle weiteren Auslegungsdaten einer Produktionsanlage bestimmt.
Somit lohnt sich ein Blick auf die Bestimmung der Anlagengröße, um eine notwendige, aber nicht übergroße Anlage zu planen.
Würde es gelingen, jedes einzelne Rezept einer Produktionseinheit zu betrachten und für jedes einzelne Rezept eine optimale Batchgröße zu bestimmen, dann wäre eine Definition der optimalen Reaktorgröße für eine Menge an Rezepten möglich.
Genau diesen Ansatz verfolgt unsere ‚Plant-Improvement-Analyse (PIA)‘. Bei der PIA wird für jedes Rezept eine ganzheitliche, betriebswirtschaftliche Betrachtung des Produktionsumfeldes entwickelt und die optimierte Batchgröße nach betriebswirtschaftlichen Gesichtspunkten definiert.
Die optimale Batchgröße beschreibt den Punkt, bei dem die Summe aus Lager- und Produktionskosten (Gesamtkosten) minimal sind (s. Abb. 1).
Welche Faktoren beeinflussen die optimale Batchgröße?
Bei der Produktion von Gütern fallen Kosten an, deren Höhe abhängig ist vom jeweiligen Energieverbrauch (Betriebsmittel wie Strom oder Gas), eventuellen Rüstkosten für Maschinen, der Arbeitszeit von Mitarbeitern oder Kosten für Laboranalysen. Diese Produktionskosten sind für jedes einzelne Rezept immer individuell zu berücksichtigen.
Neben den Produktionskosten fallen Lagerkosten an. Die Rohstoffe und Fertigprodukte müssen gelagert werden und so entstehen physische Lagerkosten und Kapitalbindungskosten.
Die Produktions- und Lagerkosten sind in Abhängigkeit der Produktionsmenge zwei gegenläufige Kostenblöcke (s. Abb. 1).
Je größer die Produktionsmenge ist, desto geringer sind die relativen Produktionskosten. Gründe hierfür können die gleiche Produktionszeit bei größerem Volumen sein oder geringere Laborkosten pro Menge. Gleichzeitig steigen die Lagerkosten bei größeren Produktionsvolumen durch mehr Bedarf an Lagerstätten und höheren Kapitalbindungskosten.
Bei der PIA wird die optimale Produktionsmenge eines Batches (optimale Batchgröße) für jedes einzelne Rezept einer Produktionslinie in Abhängigkeit der Lager-, und Produktionskosten bestimmt.
Es entsteht eine statische Simulation, die über einen definierten Zeitraum (z. Bsp. Jahresbedarf) die wirtschaftlich optimale Batchgröße für alle Rezepte berechnet (s. Abb. 2).
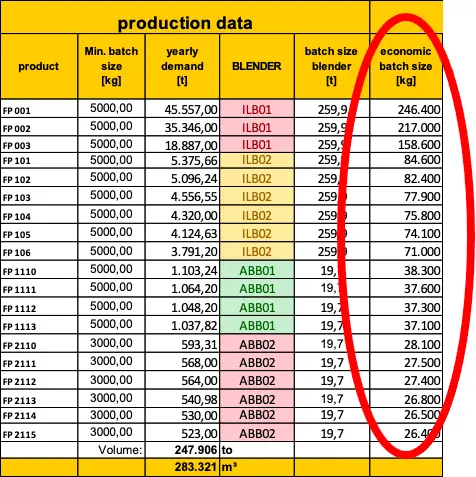
Abb. 2: Ermittlung der betriebswirtschaftlich optimalen Batchgröße nach PIA am Beispiel einer Anlage zur Produktion von Schmierstoffen (LOBP)
Rechnerisch wird die optimale Produktionsmenge bestimmt nach der modifizierten Andler-Formel (EOQ-Formel).
(Kurt Andler: Rationalisierung der Fabrikation und optimale Losgröße. Oldenbourg, München. 1929.)
In der betriebswirtschaftlichen Lehre zur Bestimmung der optimalen Lagerbestände ist die Andler Formel ein bekanntes und angewendetes Modell.
Anpassung der PIA an Nebenbedingungen
Nebenbedingungen aus der Realität können die Ergebnisse aus der rechnerischen Simulation der betriebswirtschaftlich optimalen Produktionsgröße beeinflussen.
So können bei der Definition der Batchgrößen Transportgrößen, Verpackungsgrößen oder auch Beschaffungsprobleme von Rohstoffen eine Rolle spielen und die Lagerkapazitäten bzw. die Batchgrößen beeinflussen.
Daher ist für jedes Rezept eine Prüfung der PIA-Ergebnisse unter Berücksichtigung der Nebenbedingungen durchzuführen. Erst dann werden die tatsächlichen Lagergrößen für Rohstoffe und Fertigprodukte sowie die optimalen Batchgrößen endgültig festgelegt.
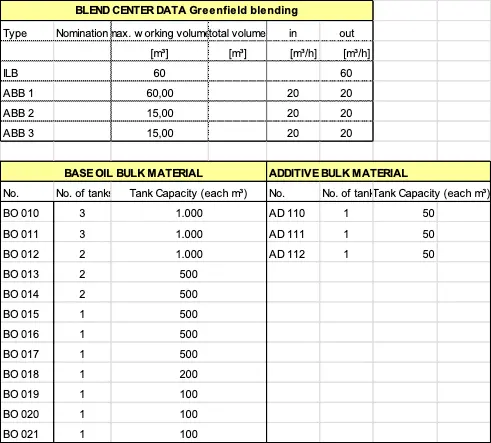
Abb. 3: Beispiel einer Zusammenfassung der realen Ergebnisse aus der PIA mit Anpassung an Nebenbedingungen
Anwendungsbereiche
Ursprünglich wurde die Methode entwickelt zur Größenbestimmung bei der Fertigung von Losstücken. Die Lagerkosten werden den Rüstkosten gegenübergestellt und die wirtschaftliche Losgröße ermittelt.
Von uns eingesetzt, wird die Plant Improvement Analye (PIA) genutzt zur wirtschaftlichen Batchgrößenbestimmung in der Produktion von chemischen und petrochemischen Produkten. In der Praxis eingesetzt, haben wir die PIA zur Auslegung von optimalen Produktionsstätten für die Produktion von Schmierölen (LOBP) und die Betrachtung von Kunstharzreaktoren.
Für beide Anwendungsfälle liegen Erfahrungswerte vor. Hier können sowohl kontinuierliche Fertigungslinien als auch diskontinuierliche (Batch) Reaktions- und Mischprozesse berücksichtigt werden.
Bei der Anwendung der PIA werden die Anzahl und Größen der Lagertanks und Verpackungseinheiten für Rohstoffe und Fertigprodukte bestimmt als auch die Größe und Menge der kontinuierlichen oder diskontinuierlichen Produktionseinheiten.
Aus der PIA-Simulation werden das Materialfluss- und das Prozessfluss-Diagramm entwickelt, in dem die Mengen und Größen der Lager- und Produktionsbehälter dargestellt und auch die Anlieferung der Rohstoffe und die Abfüllung der Fertigprodukte definiert wird (s. Abb. 4 und 5).
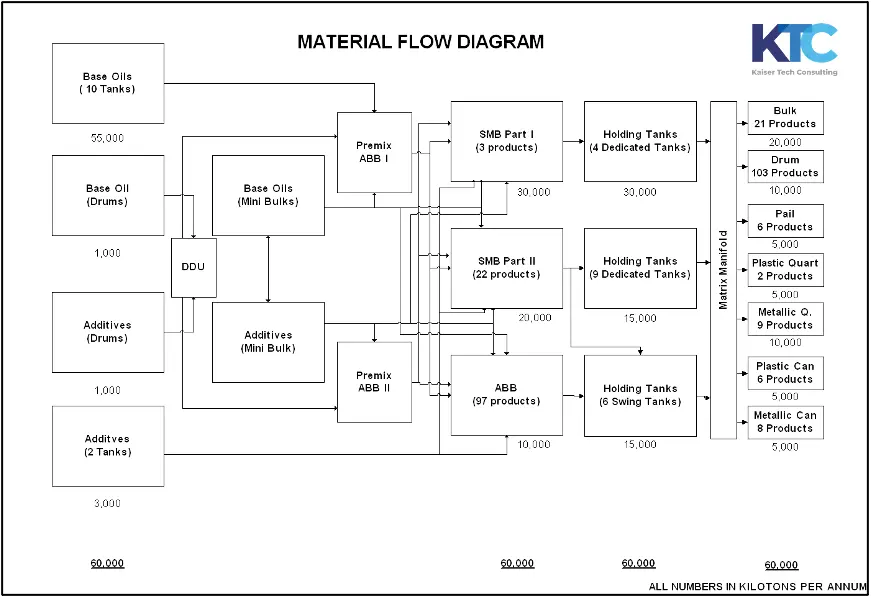
Abb. 4: Massebilanz aus PIA-Simulation für eine Schmierstoffanlage
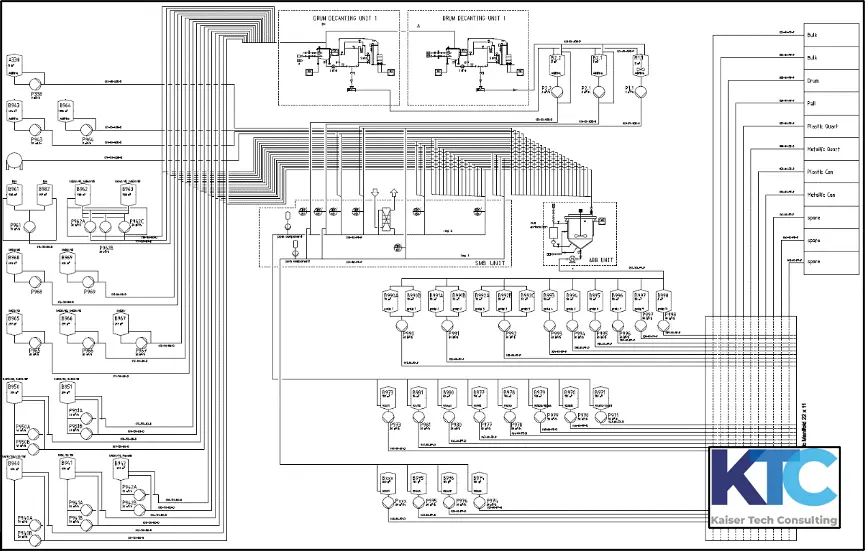
Abb. 5: Prozessfluss-Diagramm einer Schmierstoffanlage entwickelt aus der PIA Simulation
Management Summary
Die Ermittlung der optimalen Größe von Produktionseinheiten ist die Grundlage für die Planung von Neuanlagen (Greenfield) oder Produktionserweiterungen (Greyfield).
Die hier vorgestellte Plant-Improvement-Analyse (PIA) liefert eine Berechnung der optimalen Batchgröße auf Basis von betriebswirtschaftlichen Daten, deren Ergebnisse mit realen Nebenbedingungen erweitert wird.
Insbesondere im Bereich der Kunstharzanlagen (Synthetic Resin Plants, SRP) und Schmierstoffanlagen (Lube Oil Blending Plant, LOBP) ist die PIA bereits erprobt und erfolgreich angewendet worden.
Die Analyse bietet als Ergebnis die Größe und Anzahl der notwendigen Produktionseinrichtungen sowie die zugehörigen Lagerkapazitäten für Rohstoffe und Fertigprodukte auf Basis der Realdaten von jedem einzelnen Produkt einer Produktionseinheit.
Die PIA-Simulation ist die Grundlage für jede verfahrenstechnische Betrachtung und Planung einer Produktionsanlage auf betriebswirtschaftlicher Basis unter Einbeziehung von Realdaten und Störfaktoren. Eine kostengünstige, schnelle und ganzheitliche Auslegung von Produktionsanlagen.
Für weitere Informationen können Sie mich gerne kontaktieren!